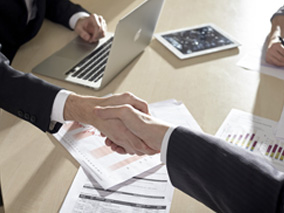
お客様より受注
材質検討やお見積り、ご相談ごとにお応えいたします。
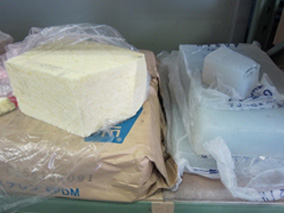
原材料の調達
ご注文を頂いた製品に必要な材料(原材料等)を、材料メーカーや商社へ発注します。
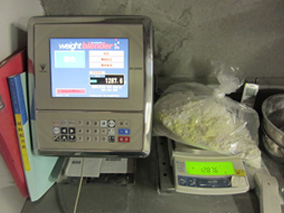
ゴム原料、薬品の計量
ゴム原料に多種の薬品を配合し、混錬作業を行います。 この薬品の配合により製品に必要とされる強度や硬さ、特性を持つ様になります。弊社では、配合指示計にて薬品計量の記録を残し、トレーサビリティーにも対応しております。
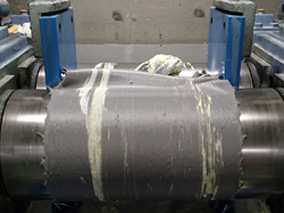
ゴム原料と薬品の混練
配合指示計にて計量された薬品を、オープンロール機もしくは、ニーダーで素練りを行い、その後混錬作業を行います。この作業により原料ゴムから加硫ゴムとなります。顔料もこの作業時に一緒に入れます。 この作業により製品に必要とされる強度や硬さ、特性を持つ様になります。
混練作業は作業認定者のみ(弊社では3名)が行います。
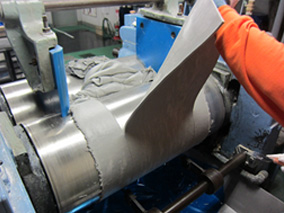
分出し
ロールで混練された材料は、裁断基準書で管理されている条件に従い、分出し(厚み)・幅だしを行います。分出しは製品重量、成型作業効率を考えられた厚みと幅でシート状にされています。
ロールに刃を当て、幅を決めます。
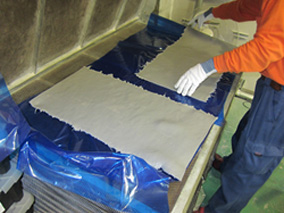
冷却
分出しされた材料は、専用の棚で冷却されます。
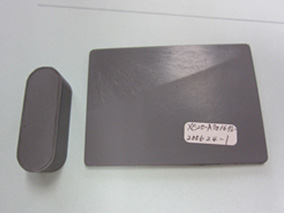
混練した材料の確認
練り上がった材料の硬度や色が基準サンプルと同じになっているか、テストピースを成型し確認を行います。
正常であれば、次工程の裁断作業へ移ります。
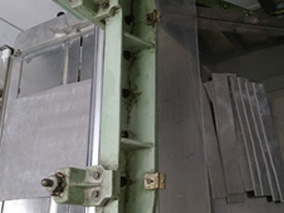
裁断
シート状に分出しされた材料を製品に必要な大きさ・長さ・ 重量でカットします。
裁断機は裁断寸法を設定する事により、定尺に連続でカットする事ができます。
裁断された材料は、製品別に表示された材料BOXに入れられ、材料間違いが無い様に管理されています。
材料の誤りは、取り返しのつかない重大なミスとなりますので、間違いが無い様、材料配膳は担当者のみが行います。
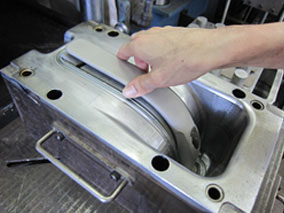
成型(仕込み作業)
お客様の要望により、その形状に加工された金型に適量のゴム材料を仕込み、弊社既定の技術指導書設定にて成型機で熱・圧力・時間をかけ加硫させます。
この製品はゴムの中に芯金が入る為、材料と一緒に金型に仕込みます。
成型機の熱で柔らかくなったゴム材料は、 プレスの圧力により金型の形状へ流し込まれます。
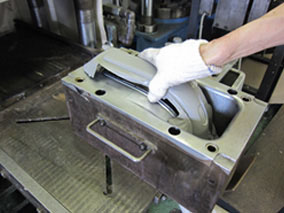
成型(脱型作業)
製品の形状・材質・季節などにより、時間と温度は細かく調整します。
規定時間の加硫後、製品を金型から取り出します。
必要であれば、恒温槽に製品を入れ2次加硫を行います。
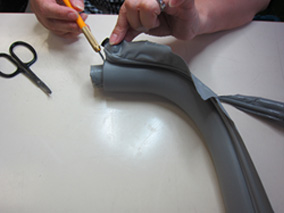
仕上げ
仕上げ作業はカッター、ハサミなどを使い、製品に不必要な部分(バリ)を除去します。
製品によっては、グラインダーやモーターを使用する物や、冷凍デフラッシャー、タンブラーにてバリを除去する場合もあります。
金型には喰い切りと呼ばれる刃が細工されており、ハサミ等が不要で、手だけでバリが取れる製品もあります。
地域の皆様に内職さんとして、仕上作業のお手伝いをして頂いております。
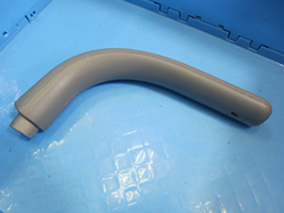
検査
バリを除去された製品を一点一葉の検査標準書に基づき検査を行います。検査項目は、寸法検査、外観検査が一般的ですが、弊社では絶縁・難燃性材料の取扱いもありますので、テスターにて絶縁性を測定したり、ゴムを火で燃やし難燃性の確認も行います。
弊社検査員は拡大鏡で製品の隅々まで細かく検査し、お客様が安心して使用して頂ける様、心がけて検査しております。
梱包